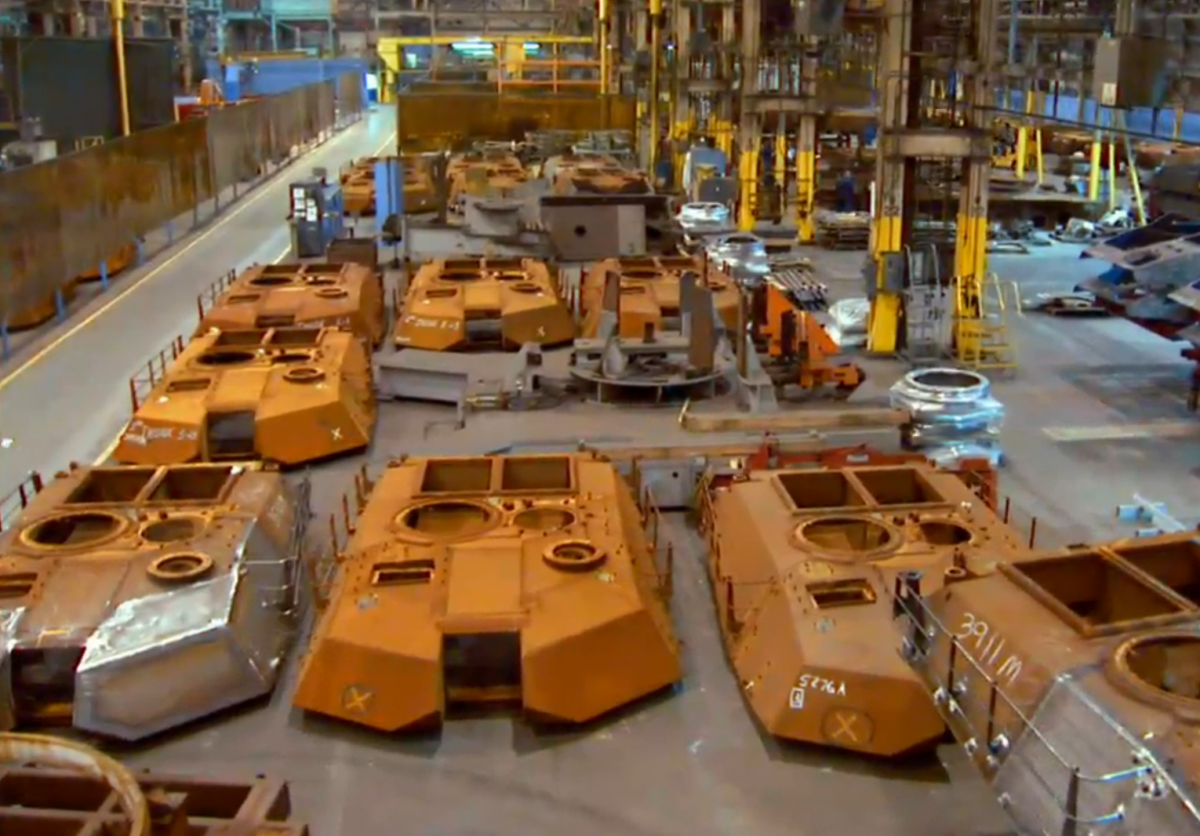
Hola a todos,
después de muchos artículos y de que siempre hubo alguna que otra pregunta sobre blindajes estaba claro que había que crear una serie entera sobre todos los tipos de blindajes. Como siempre no haré de estos artículos un doctorado científico sino que mantendré todo este asunto lo más sencillo y fácil de entender posible para aquellos que no están familiarizados con esta temática, por eso pido disculpas por si estos artículos no cumplen con los estándares científicos. La meta -teniendo los detalles relevantes en mente- es entender en lo general como este tipo de blindajes están construidos y como protegen.
Así que comenzaremos hoy esta serie con el primer y aun a día de hoy fundamental tipo de blindaje en vehículos de combate blindados : El blindaje de acero.
Comencemos…
La capacidad de tanques de batalla de sobrevivir bajo el fuego enemigo y ser casi invulnerable a una gran cantidad de armas depende en gran parte por el blindaje. La capacidad de protección del blindaje es por lo tanto uno de los pilares fundamentales de tanques de batalla y demás vehículos de combate blindados. De hecho tan fundamental que hay doctrinas que le dan la máxima prioridad a detrimento de la movilidad y/o la potencia de fuego.
En los primeros 40 años en la evolución del tanque de batalla, el blindaje estaba configurado para proteger contra proyectiles cinéticos o sea proyectiles que penetran el blindaje por pura fuerza de impacto. Por entonces el material principal a usar era el acero debido a que este tiene la capacidad de ser endurecido y moldeado. El acero usado por entonces era especial ya que se le añadían otro materiales como por ejemplo carbono, níquel y cromo entre otros para crear aleaciones de acero con mejores cualidades.
Para ver la diferencia, un típico acero para la construcción tiene una resistencia a la tracción de unos 350 MN/m² (= Mega Newton por metro cuadrado), mientras que el acero para los primeros blindajes de tanques estaban entre 850 y 1700 MN/m² y los más modernos de hoy en día tienen 2180MN/m².
Así que mucho cuidado si queréis hacer una jugada al estilo de «El Equipo A» con la plancha de acero del chatarrero, porque es muy probable que sea menos «anti-balas» de los pensado. Uffff, la nostalgia me esta volviendo ha torturar….
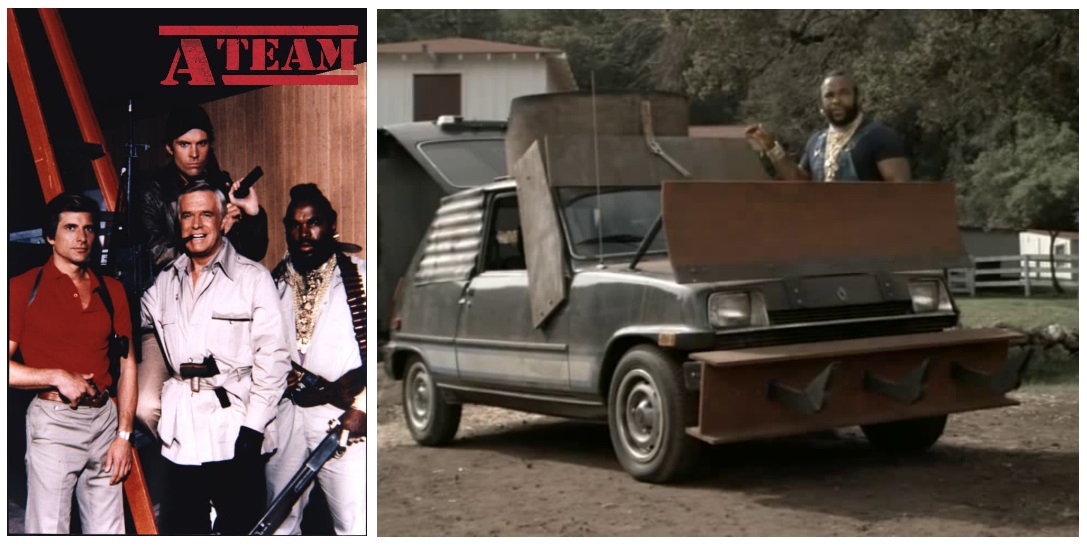
Cuando tratamos blindajes de acero hay que saber que a día de hoy existen cinco tipos de aceros: Acero colado, acero laminado, acero de alta dureza, acero de superficie endurecida y el acero-VIM/ESR. La existencia de estos cinco tipos se debe a que por un lado las características del acero dependen de la amenaza en particular, o sea contra proyectiles se requiere un acero muy duro pero contra explosivos (= Minas) un acero tenaz y flexible es mejor. Por el otro lado porque dichas características necesarias del acero se oponen las unas a las otras y además hay que desarrollar y construir el tanque dentro de unos estrictos parámetros de peso, tamaño y precio.
Resumiendo de una forma muy simple:
Cuanto más duro es el acero más delgada es la placa, más difícil es de construir, moldear, montar y soldar y vice versa. Por eso todos los avances en esta materia se concentran en crear un acero flexible y moldeable pero que a la vez es lo más duro posible.
Veamos estos cinco aceros más detalladamente….
Tipos de aceros para blindajes
El acero de alta dureza (Inglés: HSS – High hardness steel):
Este acero es de los más duros que existen y se caracteriza por una dureza que empieza más o menos a partir de los 500 en las escala de Brinell (= 500HB) o más.
Obviamente la gran ventaja de este acero es su muy alta dureza, la desventaja es que se pierde la flexibilidad por completo y eso conlleva cuatro problemas:
- Debido a que ya no hay maleabilidad solo se pueden producir placas completamente rectas sin ningún tipo de curvatura.
- Las placas no pueden ser gruesas porque la aleación de endurecimiento solo es aplicable en placas que no superan un cierto grosor.
- La sujeción de dichas placas al tanque se convierte en un detalle muy importante ya que no sirve de nada si la placa en si aguanta el impacto una munición antitanque pero no la sujeción y por lo tanto el blindaje se desploma. Inicialmente placas de alta dureza no podían ser soldadas y por lo tanto la sujeción estaba basada en tornillos o remaches. A dia de hoy si se pueden soldar pero sigue siendo un asunto delicado.
- Otro problema que persistía inicialmente es que debido a la muy poca flexibilidad y alta dureza estas placas tenían la tendencia de fracturarse cuando estaban bajo estrés cuando se intentaban soldarlas o recibían un impacto. De ahí que a veces se pegaban con otra placa de acero mas blando como soporte.
Históricamente este tipo de acero fue el primer en ser usado en los primeros tanques de la 1GM y la dureza estaba entre 420 y 650 HB y las placas solo tenían un grosor de entre 8 y 14mm porque solo tenían que proteger antes armas de infantería, ya que inicialmente no existía el armamento antitanque. En la siguiente imagen de un Mark IV vemos que las placas de blindaje están remachadas al armazón del tanque lo cual era por entonces la única posibilidad de sujetar placas de acero de alta dureza.
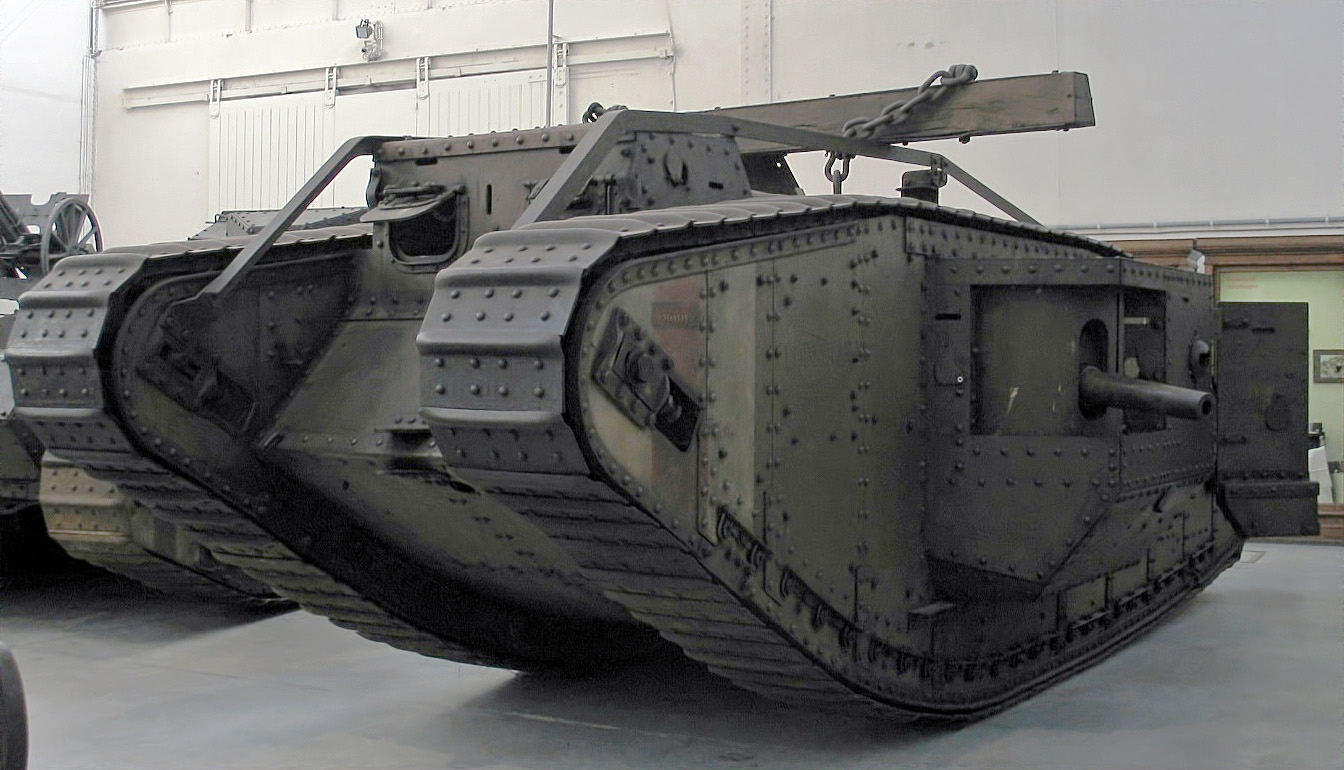
Sin embargo a partir de la época entre guerras se hizo necesario aumentar el grosor de las placas y utilizar las soldaduras como método de sujeción, así que no quedaba otra opción que reducir la dureza de las placas de blindaje.
A partir de este periodo este tipo de acero se dejo de usar como blindaje principal para tanques y no volvieron a entrar en escena hasta la década de los 60 con una aleación mejorada con una dureza de entre 500-550HB que permitía soldarlas con éxito y fue usada desde entonces con éxito en tanques ligeros. El primer tanque ligero producido enteramente de placas de alta dureza era el Cadillac Cage Stingray, usado a día de hoy en el Ejercito de Tailandia.
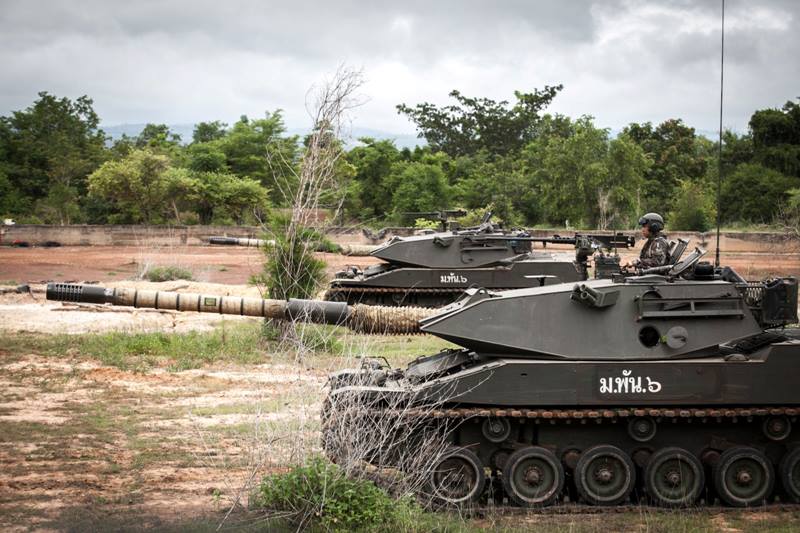
Otra peculiar diferencia es que este acero se suele usar por si mimo solo en tanques ligeros, mientras que los siguientes dos tipos de acero (Laminado y colado) se usaban muchas veces en conjunto en tanques medios y pesados.
Viendo todo esto vemos que tanques ligeros están en relación al acero que usan mejor protegidos que tanques medios o pesados.
El acero colado (Inglés: Cast Steel)
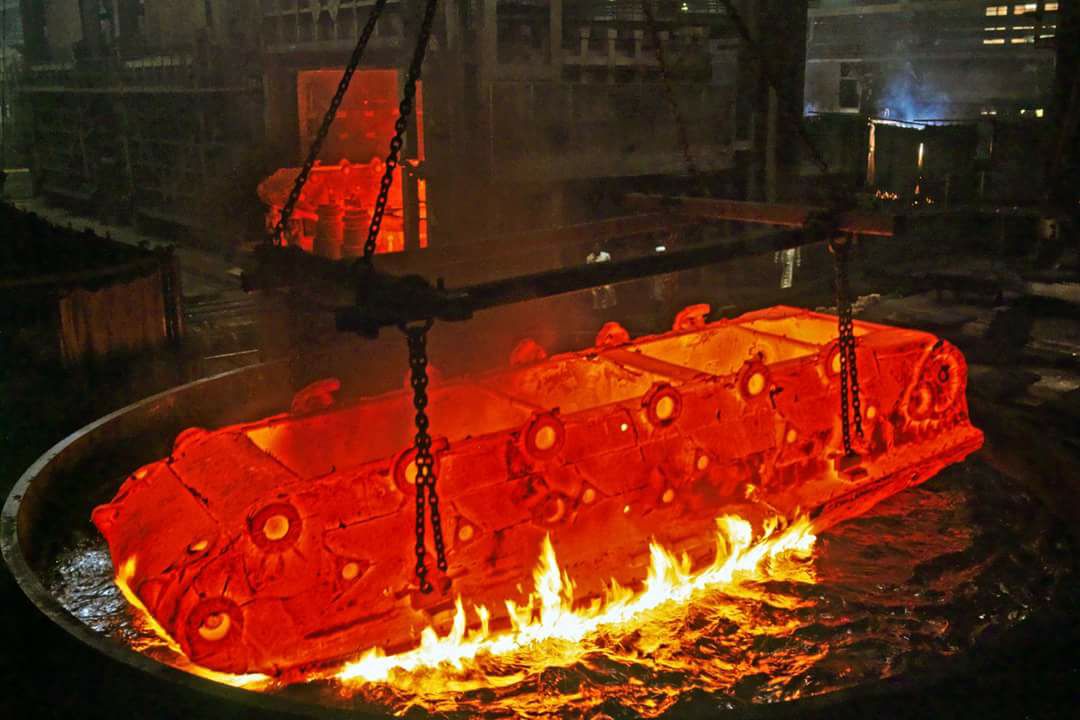
En la foto de arriba vemos el chasis del Panzer 68 hecho de acero colado y es el acero más blando de los cuatro con una dureza de Brinell que esta más o menos entre ~220HB y 300HB.
La ventaja de este acero es su muy alta moldeabilidad y por lo tanto facilita la producción de piezas de tanques en gran medida, ya que en vez de producir distintos tipos de piezas por separado para luego soldarlas entre si, lo único que hay que hacer es verter el acero fundido en un molde y cuando este se haya enfriado la pieza esta lista y solo hay que sacarla del molde para seguir con la producción, por lo tanto es un método de producción muy simple y barato.
A partir de 1950 los americanos consiguieron perfeccionar este proceso hasta tal grado que podían construir de una sola pieza el casco entero del chasis del tanque M48.
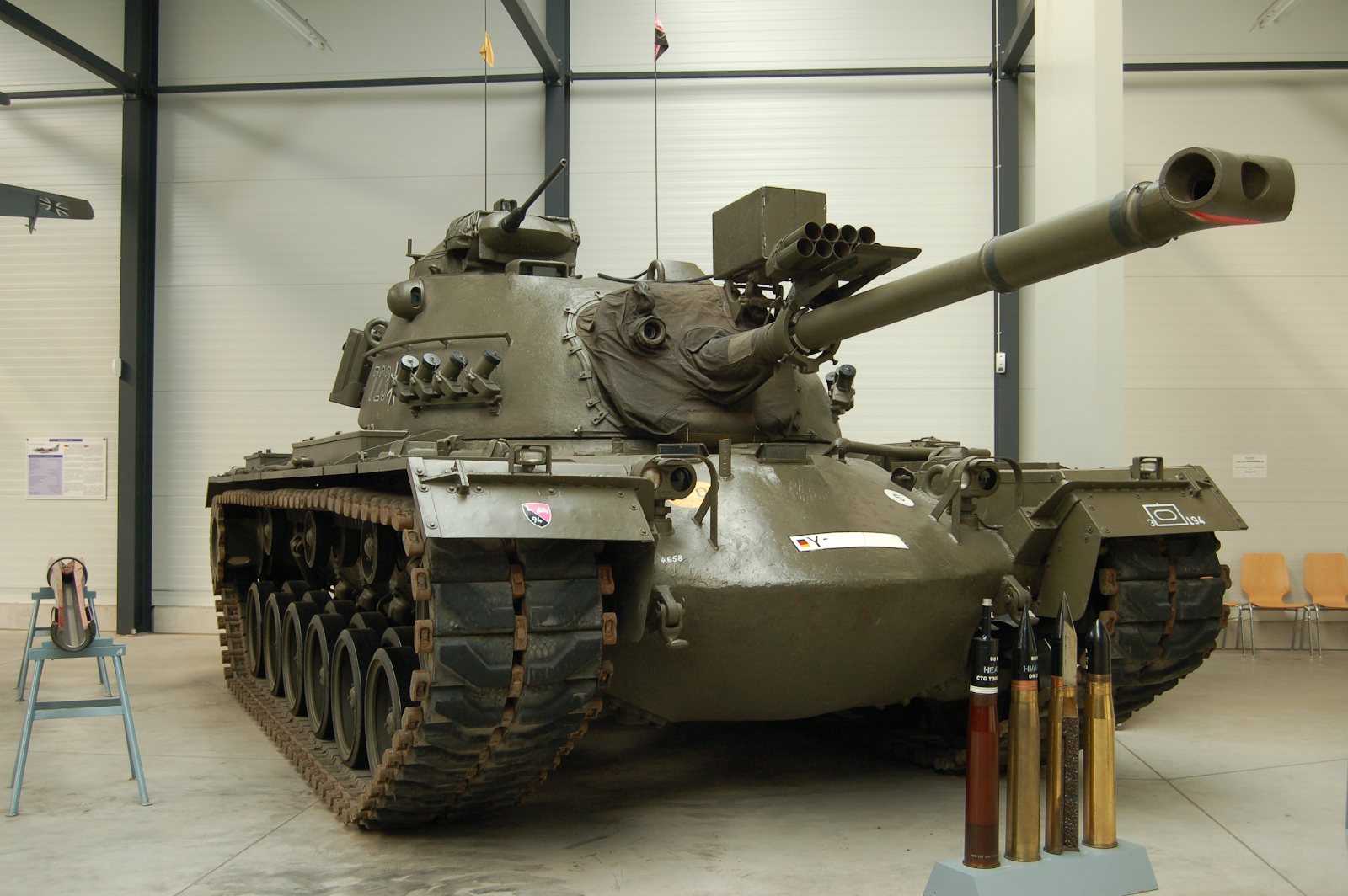
En fin no es un accidente que carros que son famosos por su fácil y barata producción sean en grandes partes de acero colado.
Las desventajas de este acero es que con el proceso de colado la calidad varia, las medidas de las paredes no se pueden controlar tan fácilmente como con el acero laminado y debido a las distintas formas de las piezas con distintos grosores se crean características balísticas más variables.
Por eso por regla de dedo se construye las paredes de las piezas con un 5% mayor de grosor para asegurar las mismas características balísticas que el acero laminado, lo cual sin embargo hacen a su vez el carro más pesado. La segunda desventaja es que debido a los formas de las piezas y los diferentes grosores de las paredes el proceso de endurecimiento – que será explicado más adelante – de las superficies es mucho menos efectivo.
Este acero y su método de producción fue introducido por primera vez en la producción de la torre del famoso tanque Renault FT de la 1GM y ya a partir de entonces hasta inicios y mediados de la Guerra Fría se construyeron una gran parte de las torres y chasis de tanques medios y pesados con este acero, mientras que durante el mismo periodo los tanques ligeros seguían siendo de placas soldadas.
En resumen, es el acero más blando dentro de la tecnología de blindajes pero tenaz, muy moldeable y barato.
El acero homogéneo laminado (Inglés: Rolled homogeneous steel):
La diferencia principal de este acero con respecto al anterior se basa en la forma en la que es producido. Mientras que el primero estaba basado en colar acero fundido en un molde, en este se crean placas de acero que luego se pasa por unos rodillos y es aplastado, el aplastamiento tiene el efecto que endurece el acero.
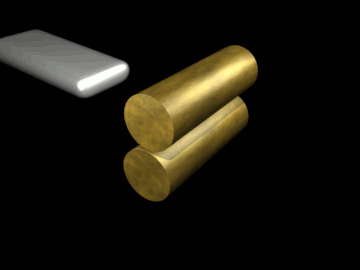
El típico blindaje RHA suele tener una dureza que esta entre los 320 y 380HB. En la siguiente foto vemos las las paredes de acero laminadas de la torre del tanque pesado Tiger I.
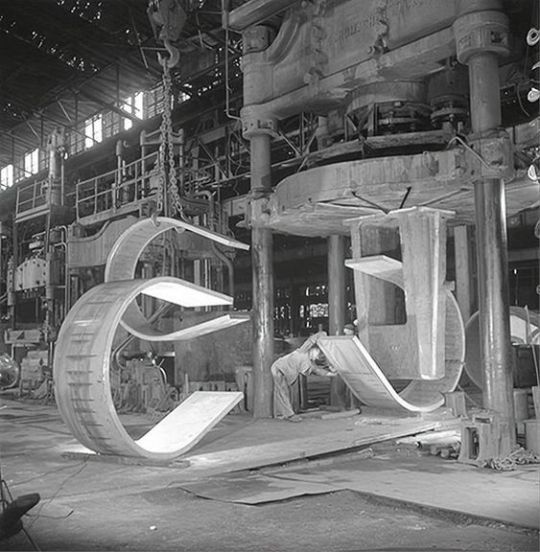
Las ventajas de este acero es que su calidad es mucho más uniforme, es mas duro y sigue manteniendo un cierta flexibilidad y moldeabilidad. Las desventajas son que el procedimiento de construcción es más caro y dura más tiempo, porque una vez que las piezas están hechas hay que soldarlas entre si y dichas soldaduras tienen que hacerse correctamente ya que tienen que aguantar todo tipo de rigores como por ejemplo impactos de municiones antitanque entre otros, o sino el tanque colapsará sobre si mismo como un castillo de naipes.
Como sabemos que a partir del inicio del periodo de entre guerras ya no se podían usar blindaje de alta dureza se introdujo este tipo de acero laminado. Inicialmente las placas eran de unos 15mm de grosor pero una vez que comenzó la 2GM el grosor aumentó rápidamente. Tanques como el KV-1 de 1939 ya tenia placas de un 75mm de grosor y para finales de la 2GM el Jagdtiger ya tenia placas de 250mm, las más gruesas jamás usadas en un tanque.
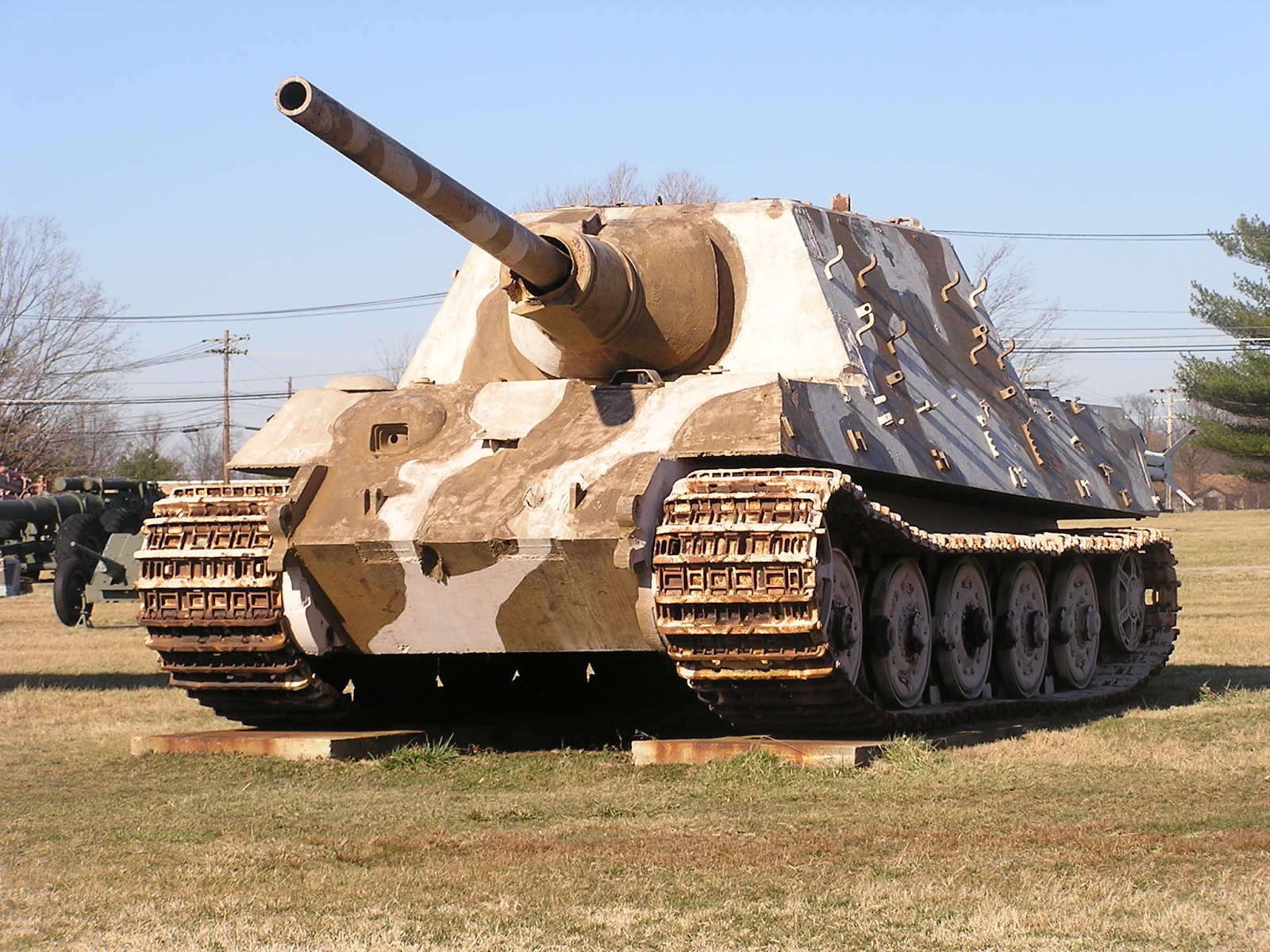
Después de la 2GM las placas no superaron los 125mm de grosor, ni siquiera el tanque pesado Conqueror de 66 toneladas llegó a usar placas más gruesas.

Teniendo estos dos últimos tipos de acero en mente vemos que una de las razones de por qué los alemanes no conseguían producir sus tanques en los números necesarios era porque estos estaban basados en acero laminado y no el más barato y rapido acero colado.
El acero de superficie endurecida (Inglés: Case hardened steel):
Este acero es la siguiente evolución ya que se caracteriza por tener dos capas, una dura y otra blanda. Este tipo de acero es un caso algo especial ya que en si no es un tipo propio sino que esta basado en los primeros tres y existe en 2 tipos distintos:
El primero es el «verdadero» acero de superficie endurecida y se trata de acero colado o laminado que ha recibido un tratamiento adicional con el resultado que la superficie – y no toda la placa – tenga una dureza bastante mayor. Un ejemplo eran las placas de blindaje de la empresa Vickers Armstrong de la década de los 30, estas tenían un grosor de 20mm y la superficie frontal tenia una dureza de 600HB mientras que la parte trasera era más blanda con 400HB, la pega era la misma que con el acero de alta dureza: la sujeción de la placa. El Panzer IIIM dispone de una placa de este tipo de 20mm y como podemos ver en la foto la sujeción es con tornillos en vez de soldaduras.
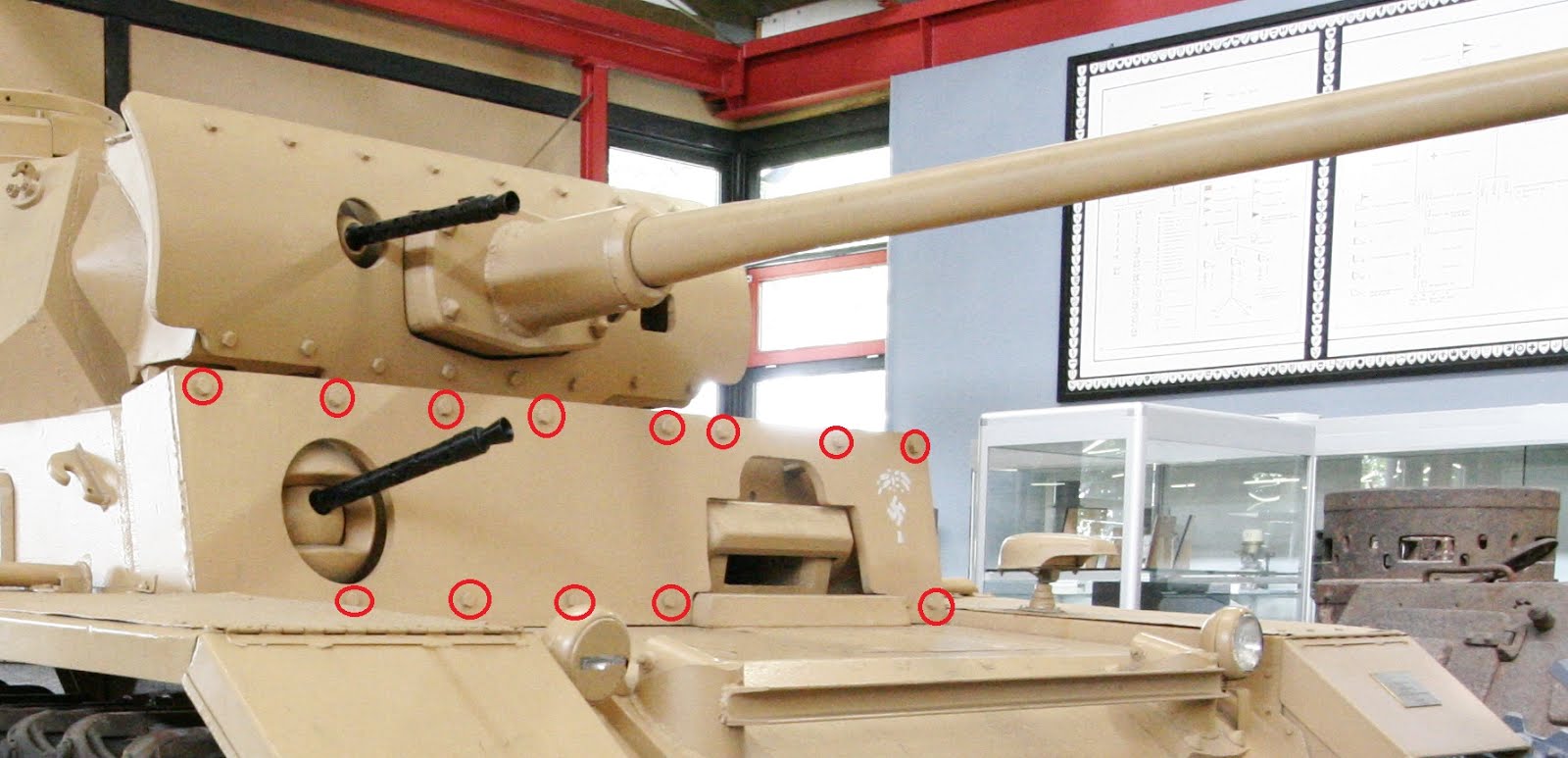
En resumen se puede decir que este procedimiento no fue muy usado durante la década de los 30 y la 2GM.
El segundo tipo surgió en la construcción de vehículos blindados durante la década de los 60 y es conocido como Acero Duplex y se trata de dos placas de acero de distinta aleación y dureza que son colocadas la una sobre la otra para luego ser unidas al pasar por un proceso de laminación similar al del acero laminado.
La gran ventaja de estos aceros de doble capa es que reúnen las cualidades de dureza y flexibilidad, la capa dura ofrece gran resistencia y daña el proyectil mientras que la capa blanda absorbe parte de la fuerza del impacto inicial y lo queda del proyectil una vez que este haya penetrado la capa de alta dureza.
Otra gran ventaja de estos blindajes es que si la placa dura esta dañada la protección sigue estando presente porque la capa blanda sigue estando fusionada con la dura y por lo tanto mantiene todo unido. La desventaja era que no se podían construir placas de gran grosor y por lo tanto no eran realmente viable para tanques más pesados, más tarde se consiguieron producir placas duplex de mayor grosor pero ya por entonces había mejores opciones.
La empresa Engesa fue la primera durante las décadas de los 60-70 en usar este tipo de blindajes en sus vehículos blindados sobre ruedas como por ejemplo el EE-3 Jararaca.
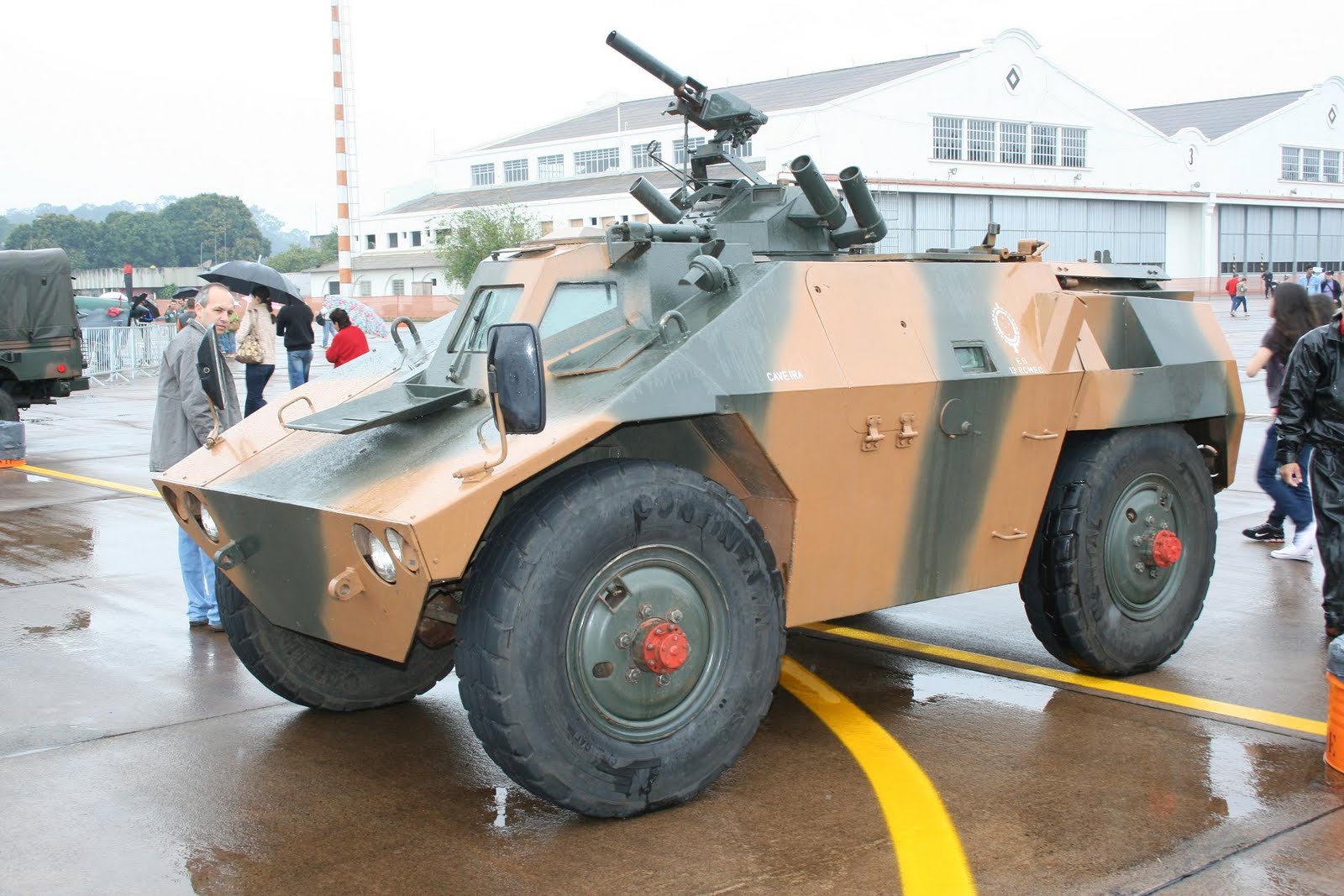
El acero colado al alto vacío y electroescórico (Ingles: VIM – Vacuum induction melting, ESR – Electro-slag remelting):
Dicho de una forma muy simple este tipo de acero se diferencia de los demás por su proceso de fundido y tratamiento, el cual consiste por un lado en fundir el acero usando un corriente eléctrica en vez del calor de un horno, por el otro lado dicho fundido ocurre dentro de una cámara al vacío y/o dentro de un baño con un material especifico.
Este procedimiento tiene como resultado un acero de gran pureza y calidad. En la siguiente imagen vemos un modelo de una maquina para hacer este tipo de tratamiento, abajo en la imagen esta la cámara al vacío donde se funde el acero a través de una corriente eléctrica.
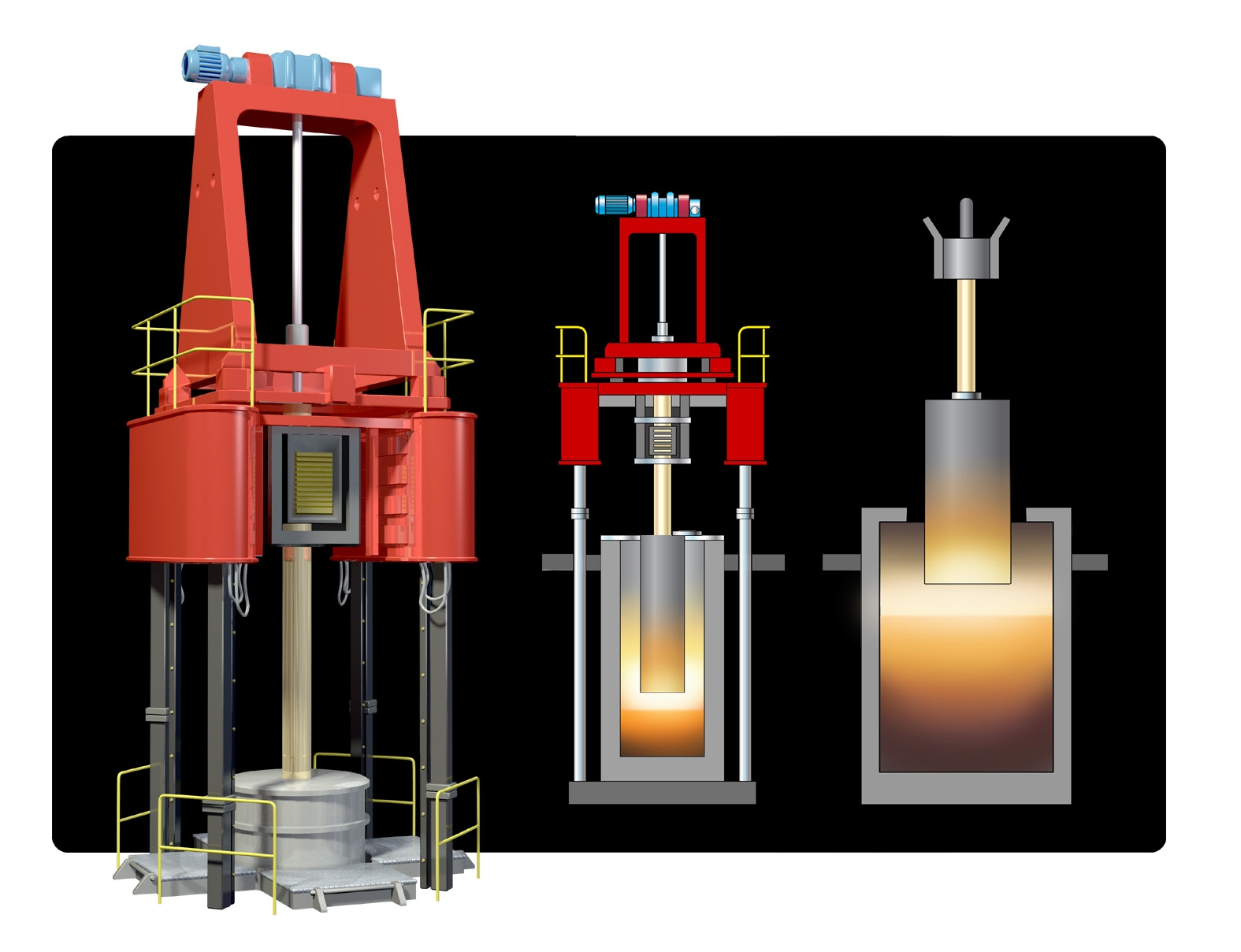
Estos son los aceros más modernos que existen, el acero colado al alto vacío es ya casi perfecto ya que por un lado ofrece la dureza (500HB+) de aceros de alta dureza pero es también flexible y se puede soldar bastante bien, la pega esta en que solo se pueden hacer placas hasta un cierto grosor y también es tan caro que muchas veces se renuncia a su uso durante la producción de vehículos blindados.
Las primeras versiones de este acero eran los fundidos al alto vacío y fueron usados durante el desarrollo del MBT-70 y sus placas tenían una dureza de 500HB pero el grosor máximo no superaba los 40mm.
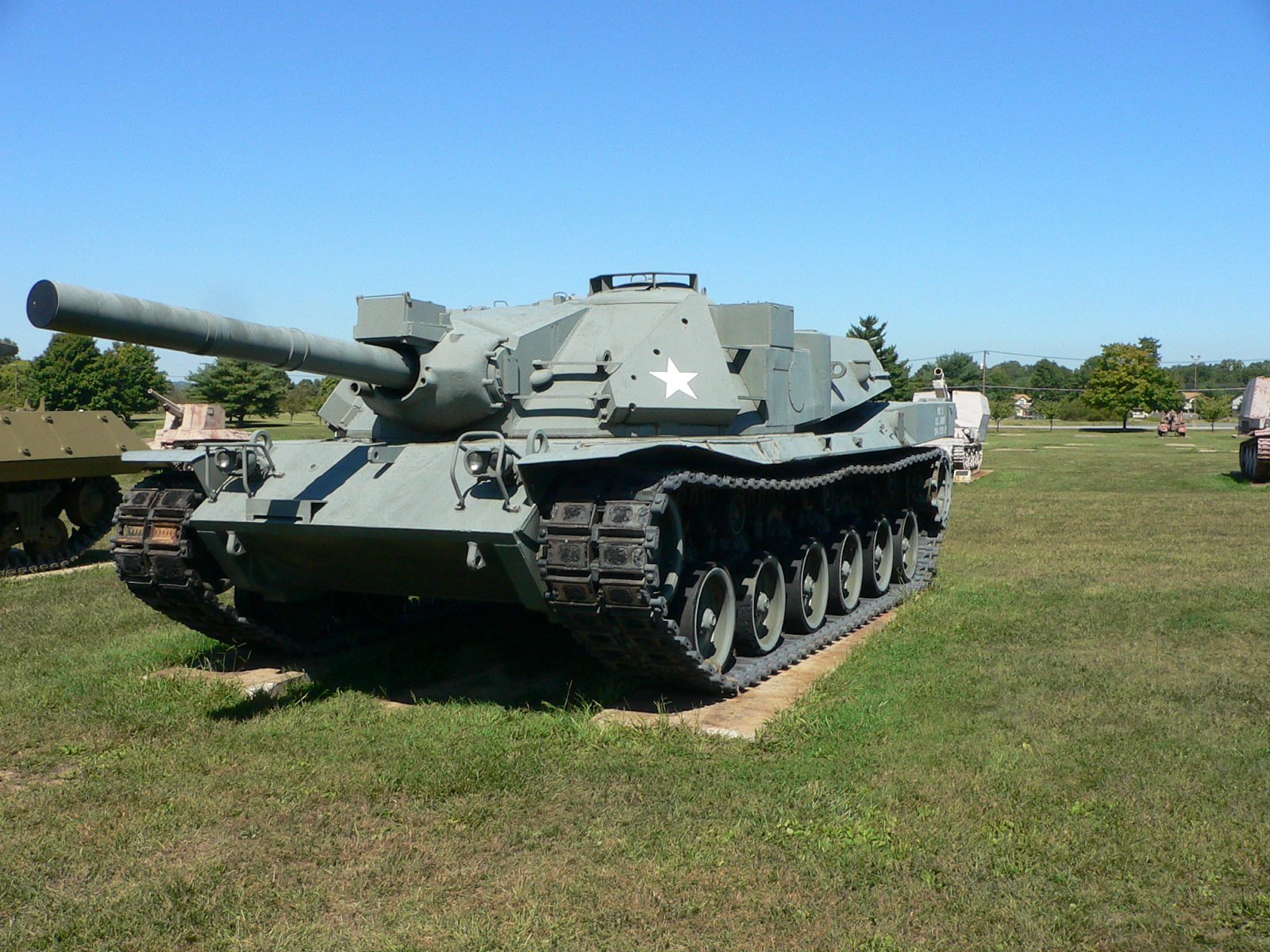
El paso evolutivo final era el acero electroescórico que empezó a surgir también durante la década de los 60 y era una revolución en la metalurgia ya que ofrecía las mismas ventajas y corregía las desventajas del acero colado al alto vació, o sea que las placas se podían hacer de mayor grosor y encima todo este procedimiento era mucho más barato.
La típica placa de blindaje de acero electroescorico es prácticamente perfecta, es flexible y tiene una dureza de 550HB. Tanques modernos como por ejemplo el T-90A son producidos con este tipo de acero, en la siguiente imagen vemos un T-90A en Siria sin su blindaje reactivo y podemos observar que la torre ya no es redonda como en los tanques rusos anteriores sino geométrica de forma hexagonal.
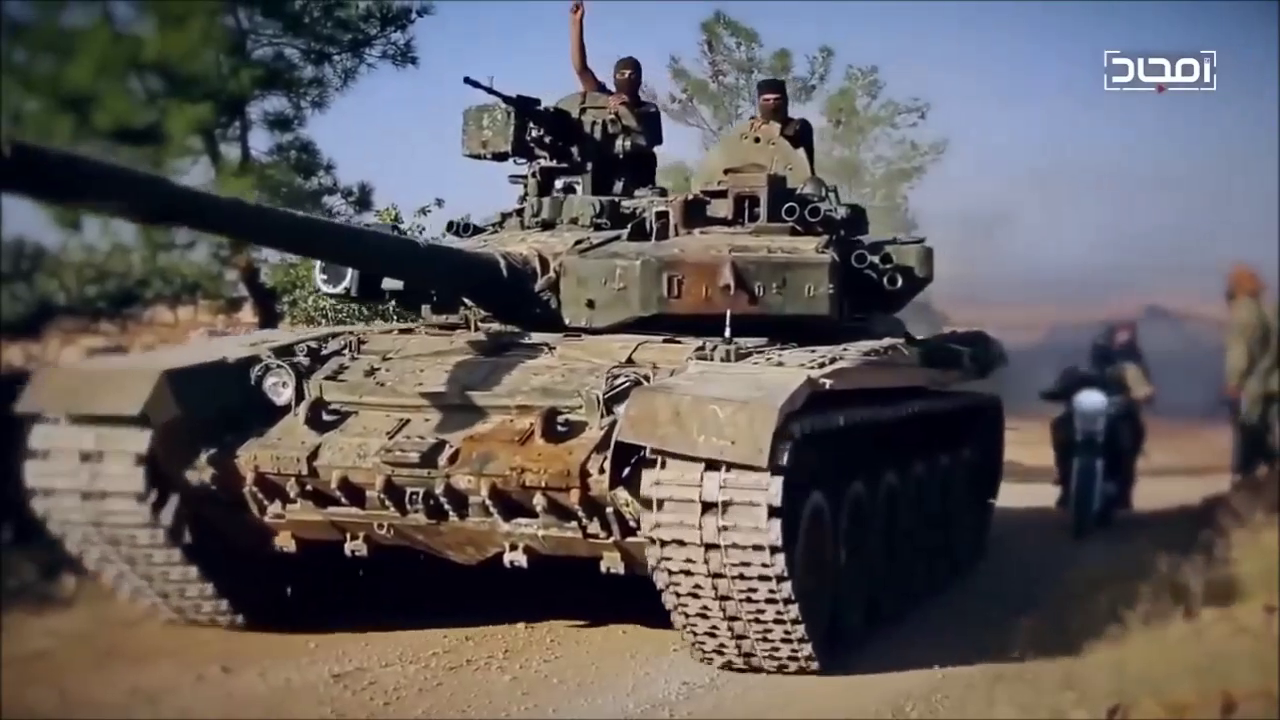
Niveles de protección de los distintos aceros:
En esta lista vamos ha ver las capacidades de los distintos tipos de acero y en la cual veremos como de gruesa tiene que ser una placa para proteger contra una bala anti-blindaje del calibre 7,62x51mm.
Como punto de orientación usaremos la típica placa de acero laminado – o sea RHA con 320-380HB – que necesita un grosor de 14,5mm para protegerse contra dicha bala.
El acero colado es el más blando y por lo tanto necesita 15,3mm o un 5% más para garantizar la protección.
El acero de alta dureza solo necesita 12,7mm o un 12% menos que la placa RHA para asegurar la protección.
Los aceros duplex y VIM/ESR que son de última generación ya solo necesitan un grosor de 9mm o un 38% menos que la placa RHA para garantizar la protección.
Como podemos ver muy bien, los aceros no son para nada iguales o parecidos. ¡¡¡De hecho entre el acero colado y el acero VIM/ESR hay una diferencia en la protección de un 41%!!!
Muy bien caballeros, aquí hemos llegado al final de este articulo y en breve habrá una segunda parte donde trataremos las distintas configuraciones de blindajes de acero y que métodos de protección usan.
Un saludo
PS: La segunda parte
Muy interesante.
En mi niñez hice una colección sobre temas militares. Y quedé con la idea de que los primeros blindajes habían sido remachados, luego soldados y finalmente fundidos, consiguiendose cada vez más protección. Ahora veo que no era esa la única razón.
me hiciste recordar mis tiempos en la universidad, ya no recordaba el tema del endurecimiento superficial en los materiales metàlicos, gracias por este artìculo en particular y gracias por tu labor en compartir esta informaciòn a fanàticos (fan boys) de los tanques como un servidor
Muy interesante articulo
enorme, fabuloso, completo sencillo y conciso. en resumen me ha encantado
Gracias, una gozada, como siempre! No todo es peso=blindaje, a más peso mejor, etc… Ilustrativo a la par que educativo 🙂
Buenisimo. Como siempre. Que placer es leer este blog
Hola a todos,
en los últimos días he estado siendo castigado por mi sentido de la profesionalidad así que voy a tener que aprender como los últimos tipos de aceros son producidos y actualizarlo en este artículo.
Mientras tanto muchas gracias por vuestros comentarios y la segunda parte ya esta subida y será actualizada y completada a lo largo de los próximos días.
Un saludo
Excelente como siempre. Un off topic, que opinión te merece este video https://www.youtube.com/watch?v=TsdkGbAv_EM las diferencias entre tanques occidentales y rusos parece enorme en este aspecto
Hola JPJ,
si hay bastante diferencia aunque es irrelevante. Me explico…
1. En dichos vídeos no sabemos que munición (La flecha tiene más retroceso) disparan y si es real o de entrenamiento.
2. Aunque el tanque haya sido sacudido eso no tiene ningún efecto sobre la puntería ya que para entonces el proyectil ya ha abandonado el cañón hace tiempo.
3. Tanques rusos son bastante más ligeros que los occidentales y están a propósito diseñados para ser más pequeños. Eso significa que tienen menos espacio en la torre para un amortiguar el retroceso del cañón y por lo tanto el resto de dicho retroceso deberá ser absorbido por la suspensión, haciendo así que este se tambalee un poco más.
4. La estabilización del cañón en movimiento no es exacta en ningún tanque porque debido al peso e inercia del armamento no es posible hacerlo de forma razonable. Por eso el sistema de tiro da el disparo libre en movimiento cuando la linea de tiro del cañón y del visor coinciden por un instante.
5. La sacudida tampoco afecta a la observación del blanco después del disparo ya que los visores tienen su propia estabilización.
En fin, todo eso da igual y queda a criterio de la tripulación si les gusta ser sacudida o no.
Un saludo
Muchas gracias Don Juan, muy claro. Crees que la mayor sacudida afecta en algo la velocidad para apuntar y hacer un segundo disparo?
JPJ,
No porque tanto el visor como el cañón están estabilizados, para estos sistemas da igual si el tanque esta siendo sacudido o si esta conduciendo por un terreno accidentado, el tiro irá donde tiene que ir.
En teoría lo único que podría pasar sería que un cargador humano sería mas lento recargando si esta siendo sacudido durante el proceso, pero tanques occidentales no se sacuden y los que se sacuden tienen cargador automático y a estos no les afecta ningún tipo de movimiento del tanque.
O sea que en resumen da completamente igual.
Un saludo
Gracias de nuevo Don Juan
Hola,
el segundo artículo ha sido actualizado.
Un saludo
Buenas! Debido al último vídeo de Youtube me he percatado de la existencia de este artículo. Acero en carros de combate, delicioso, mi pasión dentro de la pasión.
Juan has hecho un trabajo encomiable, pero veo algunas inexactitudes que paso a comentar. Como siempre todo lo dicho es con carácter constructivo. Si hay algo que apuntar, corregir o algo que necesite una explicación más profunda por favor proceded a comentarlo. No hay nadie que sepa de todo y arreglando los puntos flacos de uno es como mejor se aprende.
Intentaré explicar de una manera simple, esto con las herramientas que dan los foros sería más facil pero haré lo que se pueda.
Por último se que tengo otros dos hilos abiertos contigo Juan, pero no he podido evitar darle a este. Empecemos.
Primero, la tipología de los aceros se caracteriza por la composición química de la misma, no por los procesos. Pero en este contexto para facilitar la comprensión procede referirte tal y como haces. Así que nada, solo un apunte como cultura general.
Sobre los aceros y como son procesados. Primero hablemos de la conformación, es decir darles la firma necesaria. Todo acero en el contexto que estamos tratando empieza siendo colado. Todos, desde el acero de alta dureza al acero más simple pasando por el laminado, todos. Por cierto HSS se refiere a acero rápido, el que todos conocemos por las brocas. Acero de alta dureza deberá ser HHS, a no ser que te refieras a los aceros de alta resistencia cuyo nombre en inglés es high strength steel.
Como todo proceso el colado ha ido evolucionando y mejorando conseguiendo así mejores propiedades. Como bien comentas el acero colado al alto vacío y electroescórico no es más que un colado moderno. Según veo el más moderno usado en estos vehículos que tanto nos gustan, pero no por tal algo muy especial. Existen procesos que pueden producir aceros con unas cualidades más altas, pero supongo que no se usan por el elevado coste que conllevan.
El paso a mejores técnicas se ha dado toda la vida, como por ejemplo se pasó del Bessemer a la acería de oxígeno básico. Perdiendo así la ventaja que ofrecía el acero Sueco en comparación a otros. Pero no por ello se ha considerado un proceso de fabricación distinto, tanto uno como otro como el último son tipos distintos de colado. Yo no los pondría en apartados distintos ya que es más confuso y de así proceder se podría hacer lo mismo con todos los procesos.
El acero colado puede ser de cualquier composición (puede ser exactamente la misma que los HHS o HSS), puede tratarse de cualquier manera y puede tener cualquier dureza. También puede tener una margen de cualidades abrumadora. Como ejemplo poseo herramientas para trabajos agresivos en madera con aceros colados de alta resistencia que rondan y sobrepasan durezas de 700HB. De hecho apostaría muy alto que el chasis del Panzer 68 de la imagen que muestras tiene una dureza más alta que 300HB. Esta afirmación se basa en que en la misma imagen se ve el chasis preparado para templarlo.
El que un acero sea colado no es indicio de que tenga unas cualidades dadas, estas cambian según necesidades y capacidades. Todo se reduce a cuánto sepas y las capacidades que poseas. Así tranquilamente se puede conseguir un acero colado de mejores capacidades que uno laminado.
Sobre el porcentaje adicional en las piezas coladas en comparación con otros tipos de procesos. Tal y como bien comentas el colado de piezas es el tipo de proceso que menos preciso es. Esta es la razón por la que en toda la industria y todas las piezas se procede a dar un margen de seguridad mayor en comparación a otros procesos más exactos como el laminado. Este margen es el procedimiento estandar para entrar en tolerancias. Si hubiese la necesidad de que una pieza fuese como comentas un 5% mayor este porcentaje debería añadirse al margen de seguridad ya existente llegando así a una desviación mayor sobre el acero laminado del ejemplo. El margen de tolerancia que das es razonable que lo sea para blindajes de carros de combate, pero en la industria en general no es un dato fijo, sino que cambia según especificaciones concretas.
Para resumir, al final el colado no es más que el vertido de acero fundido en moldes para conseguir piezas de una u otra naturaleza. Al contrario de lo que normalmente se piensa con este proceder y manejando distintas aleaciones se pueden conseguir piezas de cualidades extremas.
Cuando pueda sigo. Saludos!!
Sigamos con el segundo proceso de conformación de blindajes, la laminación en caliente.
Tal y como bien explicas la laminación no es otra cosa que el alargamiento del acero (en nuestro caso a altas temperaturas) mediante presión ejercida por rodillos. Las placas que mencionas que se usan como materia prima para este proceso son piezas coladas. Esta materia prima pueden ser palanquillas salidas de coladas continuas o rectángulos de acero colados en molde llamados tochos.
Por cierto, todos loa aceros que salen de este proceso, todos sin excepcion, son aceros homogéneos laminados. Es el tipo más común de laminación, por lo que comúnmente se les llama aceros laminados. Si es algo distinto de esto es entonces que se puntualiza a lo que se refiere.
Con el laminado en caliente no se consigue ningún endurecimiento en el acero. Ni superficial ni total. La naturaleza de sus beneficios es otra y no tiene mucho secreto. Esta parte es muy visual y se puede entender fácilmente con pocas imágenes, aún así vayamos a ello con las limitaciones que tenemos.
Al hablar sobre el acero se suele empezar a explicar la estructura atómica, pero tanto ahora como en la práctica ésta información muy pocas veces es de utilidad. Así que nos lo saltamos. Lo que nos interesan son las estructuras en que se organizan los átomos, estas estructuras pueden ser visibles a veces a simple vista.
Empecemos, tranquilos que los conceptos son sencillos de entender. Después de colarlos cuando los aceros se enfrían se organizan formando estructuras cristalinas llamados granos. Algo parecido a los granos visibles en piedra arenisca. Las superficies de estos granos son las partes donde el acero reparte las fuerzas aplicadas en ella.
Cuando mayores son los granos menor superficie de contacto tienen entre ellas, por lo que menos superficie tiene para repartir los esfuerzos. Cuánto menores son los granos mas superficie de contacto poseen, por lo que los esfuerzos se reparten en una superficie mayor.
La unión entre granos posee una fuerza de cohesión. Cuando esta es sobrepasada los granos se empiezan a separar, lo que da inicio a una fisura. Cuanto mayores sean los granos menos fuerza necesitaremos para llegar a este punto, cuánto menor tamaño posean los granos mas aguantará la pieza antes de llegar al punto de ruptura.
Lo que hace el laminado no es mas que alargar estos granos. Hace pasar la granulación de una estructura parecida al de una piedra a otra más parecida a las fibras de la madera.
Con esta estructura el acero se comporta de una manera distinta. Las fuerzas se distribuyen en unas superficies aún más grandes haciendo así que el acero sea más flexible y resistente, así de simple.
Cuidado que el laminado también tiene sus peligros y el aumento de cualidades no es absoluto. Un peligro del laminado es que puede generar bandas de carburos. Estas bandas se intercalan con acero más blando. Se intercalan zonas muy duras y frágiles con zonas muy blandas, la plasticidad de uno hace que las fuerzas se acumules el las duras y frágiles zonas del acero haciendo la pieza mas propensa a la rotura. La laminación no es una varita mágica, es como todos los otros un proceso que hay que amoldarlo a las propiedades que se buscan.
Y no solo eso, tal y como hemos comentado el laminado no da un acero con unas propiedades homogéneas. Hay que tener cuidado cuando se parte de datos donde afirman que un material laminado tiene tal o cual capacidad. El acero laminado al tener la estructura dicha se comporta de distinta manera según a como se le apliquen fuerzas. Por gran margen de diferencia donde más resiste los esfuerzos es en el plano perpendicular a la dirección de laminado, la misma dirección que el largo de los cilindros. En el plano paralelo al laminado y el plano transversal a la pieza (el mismo caso de los blindajes) no lo es tanto. Esto hay que tenerlo en cuenta al valorar los ensayos de laboratorio con los que uno se puede topar.
Dicho esto, siendo todo lo otro igual, habiendo pasado por todos los procesos impecablemente y no valorando el tiempo y dinero adicional que precisa el laminado este es mejor que el colado. Pero hablamos del mundo real, aquí se pueden dar casos peculiares como el Tiger, Panther, Stug III… donde prácticamente todo el blindaje era de acero laminado. Todo menos la parte más propensa de recibir impactos, el mantelete, que eran de acero colado. No todo es blanco o negro.
Para terminar con este proceso decir que la laminación no tiene límites de medida. Es la forma más sencilla de producir planchas de acero. Todo tipo de planchas de cualquier medida que se pueda haber visto en cualquier sitio son o pueden ser producidos de esta guisa.
Saludos!
Un apunte y un comentario que se me han quedado en el tintero.
No existe una dureza dada del acero laminado. Lo tendría de modo muy general si hablásemos de la plancha como materia prima. Se podría decir que suele ser blando, pero como no todas las temperaturas de inicio y curvas de enfriamiento son iguales y existen miles de aleaciones esta puede variar sensiblemente. Varían muchísimo más si tenemos en cuenta que en aplicaciones como las de los blindajes las piezas suelen pasar por mas y muy variados procesos.
Por otra parte, he buscado ejemplos de piezas coladas usadas en vehículos con preponderancia de blindajes laminados y justo en las partes donde estos necesitan más protección cuando tenía ejemplos perfectos en el artículo. El Conqueror tenía la barcaza hecha con acero laminado pero la torre, mantelete incluido, eran acero colado. Es más, los manteletes tanto del MBT-70 como del Jagdtiger también lo eran.
Saludos!
Dándole vueltas al asunto he estado comprobando una cuestión en la red. Me parece que he encontrado indicios de donde puede venir la confusión sobre el supuesto endurecimiento del acero laminado. Hay un tipo de laminado que sí que endurece el acero y se ha usado en al menos un carro de combate, hablo del laminado en frío y del Abrams. Démosle un vistazo.
El laminado en frío es un tipo de proceso que puede usarse con la mayor parte de los metales. Consiste en laminar una plancha de acero a temperatura ambiente o una temperatura muy cercana a ella.
Para nada vale para dar reducciones de grosor como la que muestras en la imagen. Es un proceso de acabado o en su defecto uno de los últimos. Un proceso después del cual hagas lo que hagas no conviene calentar la pieza.
Consiste en dar una reducción que normalmente no pasará ni normalmente llegará al 50%. Con ello se consigue producir tensiones en la superficie las cuales son responsables de la dureza producida. Así se consiguen piezas con distintas durezas en la superficie y el núcleo. Es el mismo proceso que picar la guadaña pero hecho con otros medios.
Es una de las maneras de endurecer la superficie de la pieza, de hecho mi favorita. Como todo tiene sus problemas, como que traspasas las fuerzas que puede soportar la rigidez lo hará más propenso a la fractura y al desprendimiento de metralla o que las piezas no debidamente procesadas pueden partirse por sí mismas de una forma muy impactante para la vista.
Aún y todo es un proceso muy probado, que da buenos resultados, rápido y relativamente sencillo. Combinado con tratamiento térmico que dé elasticidad al núcleo es una combinación noble y bondadosa.
Hay que tener en cuenta que una pieza laminada en frío no solo ha sufrido este proceso. Sino que como mínimo ha sido colado, laminado en caliente y finalmente laminado en frío. Puede que esto sea lo que de pié a confusión. Ya sabéis, comentad tranquilamente por cualquier cosa.
Saludos!
Veamos el tercer y mejor tipo de conformación que se ha usado como blindaje de carros, el estampado/forjado.
Es común que sorprenda que el método más antiguo de dar forma al acero siga siendo después de milenios el mejor método para trabajar el acero. La explicación es sencilla, ¿os acordáis de los granos en forma de fibras de madera que produce el laminado? El forjado también los produce y de una mejor manera.
Al laminar los granos quedan alineados en una dirección. Si queremos juntar dos planos el método más útil es remacharlos (cosa que a nadie nos gusta) o soldarlos. Así las piezas que pueden tener direcciónes de grano distintas quedan unidas en un punto por un material que no son ellas mismas. El soldar también tiene sus riesgos, el soldado entre distintas piezas de distintos grosores como el 80mm del Tiger que vemos acampanar en la imagen del articulo no son baladí. Imaginemos piezas de mayor grosor. Pueden quedar huecos, poros, cordones mal dados… De todo.
En las piezas forjadas estos problema se ahorran con el añadido de que éstas piezas salen más robustas. Esto es debido a que en vez de soldadura en las juntas es el mismo material el que rellena completamente curvas y esquinas. No sólo eso, el alineamiento de los granos sigue la forma de la pieza pudiendo así repartir fuerzas y asumir tensiones de una manera más eficaz y repartida, haciendo el conjunto más robusto.
Y por si fuese poco. Los electrodos de soldadura suelen ser de un material distinto al de las planchas de acero que sueldan. Al hacer cualquier tratamiento que afecte a la dureza esto complica o imposibilita conseguir lo que se busca en todo el conjunto. Por lo que se suele tratar termicamente las planchas antes de soldarlas. Esto hace que terminemos teniendo tres zonas con distintas cualidades. El material a soldar previamente tratado termicamente, la soldadura y el material a soldar que ha sido calentado por el calor de la soldadura y por ello se le han alterado la cualidades. En esencia el blindaje laminado es mucho más complicado de gestionar correctamente.
Al contrario las piezas forjadas como son un solo material trates como las trates todo el conjunto responderá igual.
Por cierto la materia prima del que normalmente parte el forjado del tipo de piezas del que hablamos es material laminado. Se parte de un material bueno para hacer
Pero ¿porque no se menciona el acero forjado al hablar de blindajes? Para hacer honor a la verdad esto poco pero se hace, ha habido partes sueltas de blindajes forjadas. Pero ¿del blindaje en conjunto? Porque se ha usado poco y vivimos en una parte del mundo en el que a blindados se refiere nos han educado Anglo-Germano céntricamente.
Que yo sepa el forjado se ha usado en torres. En concreto en una parte de los FT-17 del final de la Grande Guerre y los T-34 modelo 1943 producidos en las fábricas de Yekaterinburg y Chelyabinsk. Puede que haya habido más, agradecería cualquier aportación.
Cualquiera se preguntará ¿y por qué demonios no se ha usado este tipo de proceso más veces?La respuesta radica en el precio. No de cada pieza una vez haya comenzado la producción en cadena, sino de todo el utillaje. Desde los hornos a las prensas todo es gigantesco y/o hay que hacerlo a medida. Para hacerse una idea, para producir torres de meros T-34/76 la fábrica de Chelyabinsk usaba al menos una prensa de 5.000 toneladas.
Viendo las complicaciones y gastos del forjado y laminado no es difícil entender por qué el colado haya sido un proceso tan usado durante toda la historia y por todos los actores.
Espero que esta serie os esté resultando interesante.
Saludos!
Ahora toca el proceso más importante de los aceros. El que con gran diferencia más afecta a sus cualidades físicas, más que el laminado, conjunto o no, más que los tratamientos superficiales.
Pero antes de seguir con nada. Teniendo en cuenta el esfuerzo que se hace aquí en desmitificar, destruir bulos y dar una información lo más correcta posible me ha sorprendido la nula reacción que está teniendo lo ya escrito. Por ello y por no perder el tiempo ni hacerlo perder a otros aquí lo dejo. Juan, si te interesa seguir con esto avísame, si la vida me da para ello seguiré.
Saludos
Pues a mí me ha parecido interesantísimo todo lo que has explicado, aunque una parte ya la conocía.
Una de los datos que no conocía es que el acero forjado tiene mejores cualidades que el resto. Pensaba que era de peor calidad porque se usaba para producir de forma más barata torres de T-34, la MG-42 o el PPS-43 entre otras muchas armas de infantería.
Si te encuentras con ganas por favor continúa.
Estimo mucho tus palabras JM y me alegro de que aunque sea en parte lo aquí escrito te haya servido de ayuda. Como contexto y ya que lo menciono aquí tienes el vídeo al que me he referido en anteriores mensajes.
https://youtu.be/5QSIiliAhv4
Me alegro de que menciones la estampación, ya que es un término abierto que puede llevar a confusión. Como ejemplo, no nos referimos al mismo concepto cuando hablamos de estampación en los MG-42 y PPS-43 comparándolo con la estampación que se hacía con las torres de T-34. De hecho aunque ambas estampaciones sean distintas con ambas se puede conseguir mejor material a menor costo que metiendo soldaduras de por medio.
Me explico sobre la estampación. Estampación se usa normalmente para referirse a procesos donde se ejerce fuerza a golpes y/o por medio de prensas. Pero con prensas o a golpes se pueden hacer muchas cosas. Como ejemplo y aunque no controle estas armas del todo el estampado al que nos referimos en el ejemplo del MG-42 y PPS-43 es conformado, plegado y ejecución de orificios por medio de punzones. Es decir, tomar unas planchas de acero en frío y formar agujeros por medio de punzones (embutición), hacerlas plegar por otro y por último darles la forma necesaria aplastandolos contra un molde.
El el T-34 por el contrario es un proceso parecido a este último pero el conformado se hace con acero al rojo vivo.
Todos y cada uno de los procesos mencionados se pueden agrupar bajo el paraguas de estampación. Pero los dos últimos son los únicos que se pueden considerar forjado. La diferencia es muy parecida a laminar en frío y en caliente. Pero debido a la naturaleza de la torre de un carro de combate el conformado de ella por forjado en frío nunca se ha dado.
Ganas para seguir tengo muchas JM, pero tiempo es lo que me falta.
Saludos y gracias!
ATENCIÓN , Don Juan , esto es una ALERTA y una importantísima misiva para nuestro Ministerio de Defensa Español . No es ninguna broma . Es de suma importancia . Este es el mensaje : España debe incorporarse de inmediato al proyecto AMALIA , junto a la Agencia de Defensa Europea para el estudio y obtención de nuevas estructuras metálicas para la obtención de nuevos blindajes avanzados denominados AUXÉTICOS o AUGÉTICOS , mediante un programa de I+D+i . El futuro de nuestros blindados depende de ello . Por favor , le ruego que lo comunique . Muchas gracias .
P.D. : para más información , consultar artículo aparecido hoy mismo en Defensa.com . Es un error GRAVÍSIMO no participar en este VITAL programa .
Gracias Juan por el aviso, esperemos que los politicos cambien de opinión.
¡¡¡ Bravo , bravo , Don Juan . Lo hemos conseguido !!! . De alguna manera , nuestra alerta estratégico-industrial para Defensa se acaba de producir , es oficial : España se incorpora al PROYECTO AMALIA → fuente de la noticia : Defensa.com . Enhorabuena por la ayuda y el apoyo recibido . De la investigación que se desarrolle y resulte , dependerá importantes avances en el campo de las protecciones pasivas militares y de rebote también civiles → DIVERSIFICACIÓN . Repito : INMENSAS GRACIAS DON JUAN .
Hoy es 28 de Diciembre , PERO ESTO NO ES NINGUNA BROMA . ES UNA NOTICIA VERDADERA .
Excelente, me alegro.
Recomiendo página PDF ESTUDIO DE ESTRUCTURAS AUXETICAS SOMETIDAS A IMPACTOS de la Universidad Carlos III de Madrid . Dossier de estudios completos acerca de la naturaleza y comportamiento de estos materiales polimericos y también metálicos . Os servirán de referencia y guía para comprender de que se tratan .
Muchas gracias por el aviso.
Otra página interesante de visitar es en el blog de Eduardo García , Proyecto de Prodintec para Defensa : impresión 3D de materiales auxéticos . Llama profundamente la atención la fecha de inicio de estos estudios y de este programa a finales de 2018 , desconociendo los resultados y conclusiones generados durante el mismo . Además , tiene la peculiaridad de haber sido ya por entonces incluído en el listado de proyectos seleccionados en el programa Coincidente y convocado por la DGAM . Por el contenido de la página , aunque escueto , se intuye la determinante importancia de su inherente finalidad . Don Juan , tal vez podría Usted contactar amable y cordialmente con este Señor y averiguar de primera mano el alcance de este interesantísimo proyecto e incluso tal vez podría realizarle una entrevista personal que para su propia persona y como no , para su blog ,este blog , tendría un valor incalculable y un documento de una relevancia extrema en la tecnología más avanzada en la fabricación de blindajes de última generación del tema que nos ocupa . Esto es sólo una sugerencia , una idea que a lo mejor podría serle gratificante y muy de su interés . Para finalizar , aprovecho la ocasión para enviarle un cordial saludo y para felicitarle la Navidad y que el nuevo año le traiga mucha salud y prosperidad .
Muchas gracias Juan, definitivamente lo tendré en mente, pero creo que aun tengo que crecer más para que pueda ser relevante para este señor.
Un saludo
Artículo muy bueno y completo, de fácil compresión para los no iniciados,un error gramatical » ¡¡¡De echo entre el acero colado y el acero VIM/ESR hay una diferencia en la protección de un 41%!!! en esta frase, se te olvidó poner una «H» en echo.
Gracias por el aviso Swell.